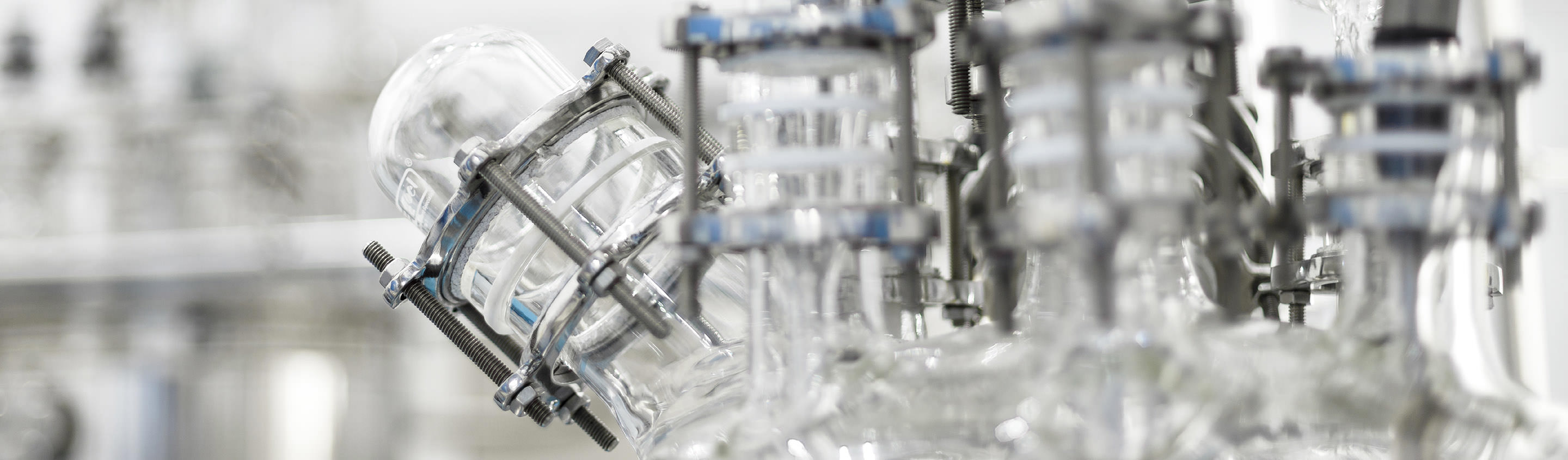
At Aragen, small molecule API manufacturing has been our expertise for two decades, covering all phases from preclinical to commercial. Our philosophy is to not operate just as a service provider; we operate as an equal partner committed to making your API manufacturing project a success. We are proactively ready to tackle any challenges that may arise with a “expect-the-unexpected” mindset.
With a collaborative approach and an unwavering commitment to cGMP standards, Aragen stands uniquely qualified to assist you in delivering a reliable supply of API, built on safe and robust processes. Our extensive capabilities in commercial API manufacturing allow us to seamlessly transition your project from development to scale-up and eventual commercial production. Aragen offers a streamlined technology transfer process, providing consistent support throughout the manufacturing journey, ensuring your project’s success every step of the way.
Manufacturing Facility – I in Nacharam, Hyderabad:
Our state-of-the-art manufacturing facility boasts 15 years of excellence in the industry. Designed to meet the highest standards, our facility includes:
Quality Control Lab: A fully equipped lab including advanced instrumentation, a wet lab, and stability chambers adhering to ICH guidelines.
Description | Block | No. of reactors | No. of Centrifuges | No. of Driers | Volume |
---|---|---|---|---|---|
Large Scale Manufacturing
|
Block-A & Block-B | 24 09 |
10 06 |
12 07 |
47250 L 19900 L |
Pilot Plant & Large-Scale Manufacturing | Block-C | 20 | 08 | 07 | 43630 L |
Kilo Labs | R&D Block-D | 12 | 12 | 03 | 2313 L |
High Pressure & Special Reactions
|
Block-E | 12 | 03 | 02 | 38200 L |
Custom Synthesis
|
Block-F | 21 | 06 | 10 | 17720 L |
HPAPI facility | G-Block | 3 | 0 | 1 | 310 L |
TOTAL | 7 | 101 | 34 | 42 | 169,323 L |
Certifications /Accreditations :
Our state-of-the-art manufacturing facility is designed to meet the highest standards of quality and efficiency, ensuring we deliver top-notch products to our clients. Here’s a closer look at our capabilities.
S.No | Description | Block | No. of reactors | No. of Centrifuges | No. of ANFDs | No. of Driers | Volume |
---|---|---|---|---|---|---|---|
1 | Large Scale Manufacturing
|
Block-A1 | 28 | 08 | 04 | 09 | 79000L |
2 | Large scale manufacturing
|
Block-A2 | 15 | 02 | 03 | 01 | 105000L |
3 | Kilo Labs | Block-B | 5 | 03 | 0 | 02 | 1600 L |
4 | High Pressure & Special Reactions
|
Block-C | 3 | 0 | 0 | 0 | 7000 L |
Total | 51 | 51 | 13 | 07 | 12 | 192,600 L |
Salient features:
4 GMP Manufacturing Blocks: Equipped with 51 reactors, including glass lined, Hastelloy, and all-glass reactors, with a total reactor volume of 192.6 KL. Our diverse reactor types enable us to handle a wide range of chemical processes.
Hydrogenators: We have two 1KL and five 5KL fully automated hydrogenators, featuring safety interlocks and a maximum operating pressure of 25 bar, ensuring safe and efficient hydrogenation processes.
Clean Rooms and Cryogenic Reactors
Clean Rooms: Our facility includes 2 clean rooms (Class 100,000) dedicated to the production of finished products, maintaining high standards of cleanliness and quality control.
Cryogenic Reactors: With two cryogenic reactors (2KL and 4KL), we are equipped to handle low-temperature reactions, ensuring precise control over critical processes.
Supporting Equipment and Systems
All supporting equipment like filters, dryers, ANFD (agitated nutsche filter & dryer) with safety interlocks.
Production Streams
3 Production Streams: Our facility supports high, medium, and low volume projects, offering flexibility to meet the varying demands of our clients.
Storage and Handling
Warehouse Facilities: Equipped with a cold storage room (2 to 8° C) and a controlled temperature room (NMT 25° C), along with a 350 KL bulk solvent storage capacity. Our warehouse also features an RLAF facility for the safe sampling and dispensing of raw materials.
Specialized Equipment
Gravity Chromatography Columns: We use two gravity chromatography columns (450mm and 600mm diameter) for the separation of isomers and products, ensuring high purity and quality.
API Processing Capabilities:
Large Scale Manufacturing (Class-100,000):
Module-1:
Module-2:
Small Scale Manufacturing (Class-100,000):
Certifications /Accreditations