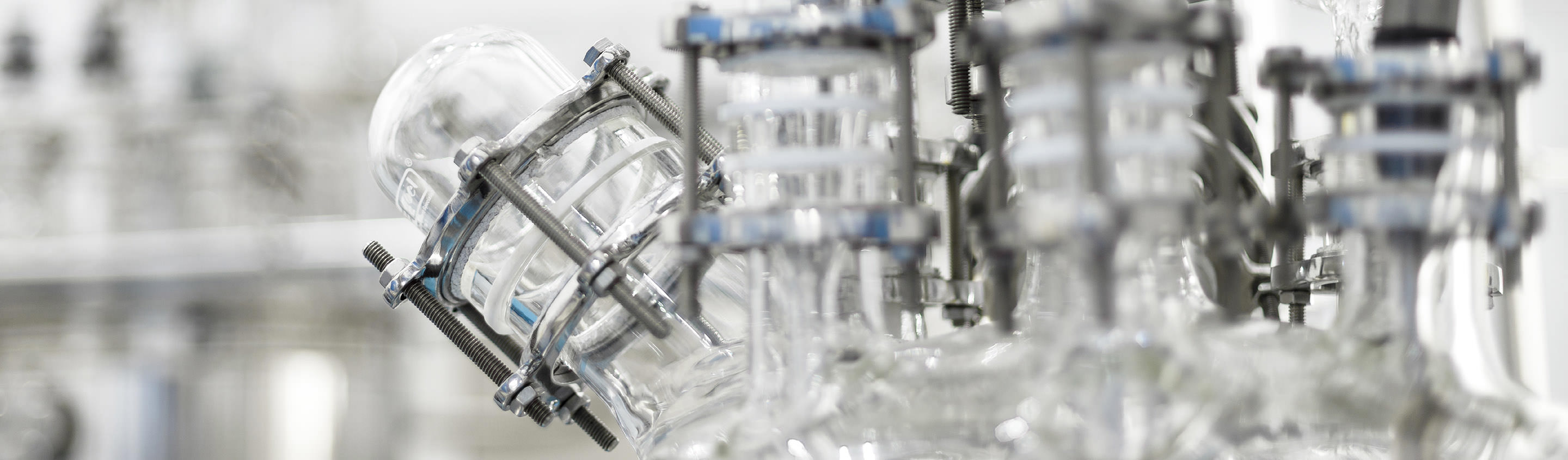
The increasing emphasis on high-potency active pharmaceutical ingredients (HPAPIs) within pharmaceutical development, fuelled by the demand for specialty drugs like oncology medications, has underscored the need for a secure capability to manage and contain these hazardous substances.
At Aragen, we have a proven history of reliably developing and manufacturing high-potency APIs and compounds for our clients. This includes a diverse range such as immunosuppressants, cytostatic/protein kinase inhibitors, ultra-potent cytotoxic drug substances, drug linkers, PEG and cyclodextrin polymeric conjugations, and toxins for antibody drug conjugates (ADCs). Our expertise extends to the development of various HPAPIs, including those classified as ultrapotent. Our cross-functional high-potency teams, comprising experts in chemistry and toxicology, collaborate closely with your development team to ensure the safe and effective development and manufacturing of your compound. Trust Aragen for a dependable partner in navigating the complexities of high-potency API development.
High Potent API handling capabilities
S.No | Occupational Exposure Band | OEL (μg/m3) / PPM | Lab | Plant |
---|---|---|---|---|
1 | Category 1 | > 1000-5000 | Working Lab with fume hoods and Analytical lab | Kilo lab Non-potent GMP/ non GMP plant |
2 | Category 2 | 100 – 1000 | Working Lab with fume hoods and Analytical lab | Kilo lab Non-potent GMP/ non GMP plant |
3 | Category 3 | 10 – 100 | Working Lab with fume hoods and Analytical lab (Flexi isolators) | Kilo lab Non-potent GMP/ non GMP plant with appropriate measures in place |
4 | Category 4 | 1.0 – 10 | HPAPI lab | HPAPI manufacturing facility |
5 | Category 5 | < 1.0 – 0.1 | NA | Vizag |
HPAPI facility at Hyderabad, India
Dedicated HPAPI facility for handling potent compounds in small scale which are having OEL value: 1-10 µg/m³ with 50 L & 10 L All Glass Reactor
S.No | Equipment | QTY |
---|---|---|
1 | ISOLATORS (Sampling & Dispensing, Drying & Sieving) (OEL4) | 2 no. |
2 | Rotavapor ( 20L) under Low Level Fuming Hood | 1 no. |
3 | All Glass Reactor (50 L) under Low Level Fuming Hood | 1 no. |
4 | All Glass Reactor (10 L) under Low Level Fuming Hood | 1 no. |
5 | De- Toxification Reactor (250 L) | 1 no. |
6 | uckner funnel under Low Level Fuming Hood (8 ft.) | 1 no. |
HPAPI Facility : Unit-II, Vishakhapatanam, India
HPAPI facility at Vizag, India
Unit Operations/ Controls | OEB4/5 (1– 10 & <1 µg/m3) |
---|---|
Sampling/Dispensing | Sampling and Dispensing through Isolator |
Liquid charging/Transfer between equipment | Closed system transfer, Gravity transfer, LEV provision during all vapour generation operations |
Solid material charging | Charging through Isolator |
Material discharge from Reacto | Above charging systems shall be used to different capacity reactors to have closed charging and transfer. Batch size shall be fixed based on process volumes. Max capacity: 2000 L |
Filtration & Drying | ANFD with Isolator for both filtration and drying operation Approximately 50 kg of material can be manufactured with the ANFD, capacity of 0.5 KL |
Milling & Sieving | Milling, Sifting and packaging inside Isolator with weighing balance |
Scrubbing System | Dedicated scrubber is connected to Isolator and negative pressure will be maintained inside Isolator |
Control at exit of people | Mist showers are provided in Air lock room |